What is involved in the environment stress screening for PCB manufacturing?
By Kelley mak
Ronkonkoma, New York
March 5, 2014 11:21pm CST
An extremely crucial part and process that falls under PCB designing and manufacturing is the reliability testing. As the name suggests, this procedure determines the correctness of PCB design and how well it will be able to withstand harsh conditions, deliver desired output and whether it has any faulty points or not.
ESS or environment stress screening is the most important tool under this type of testing. It exposes the board design to a variety of environment stresses and conditions to see how well it encounters those situations. The kind of stresses, a design is generally exposed to would be vibrations, power cycling and rapid temperature variations.
It helps in identifying any hidden and unknown defects and faults in electronic product design and structure, so that the team of engineers could work on those faults and flaws before finalizing the design and product. Electronic devices, gadgets and products have become an essential part of every modern industry. ESS gives the makers of electronic devices, gadgets and equipment a chance to look deeper into the layout and work on the design before going ahead in the production line and actual development of the product.
Before beginning with screening, the electronic manufacturer must first determine the type and number of flaws and defects, the design is most likely to have and the maximum acceptable number of defects. The aim of this testing is not to remove those latent defects, but to recognize them and put the type and number of flaws into a category which is acceptable.
Manufacturers that work on contractual basis make sure to implement ESS testing and provide their clients with the resulting recommendations and data. They make use of certain software applications for this purpose in order to draft the data that explains the failure of product during the testing phases. Below mentioned are some major points that you can expect to find in one such report.
· List of components that failed
· Time and date of failure
· Tests that caused the failure
· Tester’s name
· A description explaining the symptoms of failures
· Some additional important information associated with the failure
The last phase in PCB testing is monitoring which is generating reports and comparing the results of ESS with the set expectations. The parameters considered during comparison can vary as per the product and components under testing. However, some common parameters are:
· Screen strength
· Defects remaining
· Incoming defects
· Trend analysis
Designing and implementing a good testing process such as ESS is beneficial in more than one way, whether applied during the initial electronic productdesign stage or at any later stage of production.
No responses
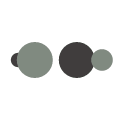