The challenges of producing compact flanges for stainless steel flange manufacturers
By crystal
@crystal42316 (69)
Los Angeles, California
August 22, 2014 3:19am CST
Traditional flanges such as ANSI, DIN and BS all rely on a dynamic joint which, when bending forces and tensile loads are applied, become loose and weak. The gap created by the raised face introduces corrosion problems particularly to the bolting aspect, which is a particular issue in critical environments as the design actually depends on the large bolt forces to maintain gasket integrity. China valve supplier
The initial cost of the higher performance compact flange is inevitably higher than a regular flange due to the closer tolerances and significantly more sophisticated design. Subsequently the product tends to be used in environments where the cost of maintenance or the consequences of leaks are particularly undesirable. By way of example, compact flanges are often used in oil and gas subsea or riser applications, cold work and cryogenic applications, gas injection applications, high-temperature applications, and nuclear applications.
As stainless steel flange size and pressure requirement increase the bolting requirement becomes increasingly heavy and complex resulting in high procurement, installation and maintenance costs. Large flange diameters in particular are difficult to work with, and inevitably require more space and have a more challenging handling and installation procedure, particularly on remote installations such as oil rigs. valve and fitting supplier
No responses
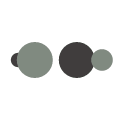