Why customized PCB boards are preferred over readymade ones?
By Jenny B
@pcbassemblydepot (23)
Morganton, North Carolina
September 11, 2014 2:11am CST
In the efficient functioning of electronic equipment, PCB (Printed Circuit Board) has a major role to play. The board comprise of electronic components that are etched on conductive pathways and tracks with a copper sheet.
Considering the rising demand of industries in today’s time, designing of PCB’s has entirely changed. Readymade boards are a thing of the past now, as customized boards are preferred these days, because of the compact design, convenience, efficiency, and functionality they provide. Moreover, these boards are stronger than readymade ones because of numerous holes drilled into it that makes it weaker for the running application of equipment.
Following are the PCB layout services carried out to design the board:
1. Jot down all tools and materials
Before heading towards creating the board, tools and materials are to be gathered, which are as follows:
Tools:
· Drill
· Iron
· Laser Printer / Photocopying Machine
· Latex Gloves
· Eye Protection
Materials:
· Etching Solution (Ferric Chloride)
· PCB Board
· Small Piece of Cloth
· Sanding Paper
· Fine Tipped Marker
· Ruler
· Glossy Paper
2. Creating design
Before making customized board, it’s important to prepare a layout, so that expert can work accordingly. PCB designing software is used for this purpose.
3. Printing of layout
Once design is made, a printout should be taken on a glossy paper via a laser printer or photocopying machine.
4. Ironing of design on board
To create the exact designed layout board, experts need to iron the layout on the board via a hot iron machine. Depending on the paper quality, which is used for layout, the iron machine temperature should be set accordingly. For example, if paper is thick, temperature should be at highest point and if not, it should be set on medium.
5. Rubbing paper off the board
Paper needs to be removed from the board. This is done by soaking the board into water for about 2 to 5 minutes. Till the time paper doesn’t become soggy, it is rubbed well under the water. However, experts make sure to rub gently so that ink on the board doesn’t get removed.
6. Sawing the excess board
After paper has been removed, excess board is to be sawed and edges of the boards are to smoothen with help of sanding paper. Finer is used ate the end for giving it a finished look.
7. Clean and etch the board
Excess paper or board is removed off well and then etched with an etching solution called Ferric Chloride.
8. Rinse the board
To clean the etching solution properly from the board, PCB is rinsed under the tap water.
9. Drill the holes
Lastly, drilling is done with a drilling machine on the copper side and cleaned well before soldering the components on it.
No responses
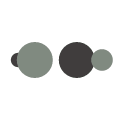