i need a dryer for straw and sawdust. Does anybody now about?
By constaanta
@constaanta (571)
Germany
October 13, 2006 9:40am CST
Farmers are using straw dryers. I want to dry 2000 kg sawdust per hour. Who can explain to me the principle of the straw dryers and give me websites for this technology?
1 response
@majorsree (575)
• India
23 Oct 06
Straw Management & Rice Drying-75
Project Leader and Principal UC Investigators
R.A. Kepner, Machinery and Costs for Soil Incorporation of Rice Straw and Stubble
T.H. Burkhardt
G.E. Miller, Jr.
J.B. Dobie, Residue Utilization for Feed, Energy, Manufactured Products
Brian C. Horsfield
P.S. Parsons
George E. Miller, Jr.
MANAGEMENT AND UTILIZATION OF RICE STRAW AS A RAW MATERIAL FOR FEED, ENERGY, MANUFACTURED PRODUCTS, OR OTHER USES - RICE HARVESTING
For rice straw to be economically useful, practical methods of collecting it in the field and assembling it at central points must be developed. UCD agricultural engineers participated in research projects on straw residue management. The objectives and accomplishments follow:
þ STRAW GATHERING SYSTEMS:
Comparison of three straw gathering systems showed that the standard pulled rectangular baler had the greatest capacity per hour with a well developed bankout and handling system, but was limited to operation under ideal field conditions and was highest in cost (about $20.50 per ton for baling, roadsiding, and placing in farm storage). Least expensive was the standard tractor-drawn big-roll bale system (about $9 per ton placed in farm storage). It had a field capacity of about 6 tons per hour, and also was limited to good field conditions. The new experimental self-propelled track-mounted big-roll baler cost about $12.20 for baling and handling into farm storage and was similar in capacity to the pull-type big-roll baler under good field conditions. It could operate in wet field conditions also, though it was reduced to 4 or 5 tons per hour. The wetter straw and consequently heavier bales give an apparent higher capacity, but less acreage is gathered per hour. The normal dry weight of big bales of rice straw is 800 to 900 pounds.
Under ideal field conditions a 3-wire standard baler has about 20% greater capacity than a big-roll baler. A proven system for banking-out and stockpiling the rectangular bales works well and at reasonable capacity (about 12 tph) under good field conditions. Even so, field conditions can often prevent use of this equipment, and rectangular bales are very susceptible to damage if not removed from the field before appreciable rain falls.
Present commercial equipment for handling and roadsiding big bales is not suited to rice-field operations. The system used to handle these bales from the pull-type baler was slow and cumbersome, with a capacity of 6 to 8 tons per hour, depending on length of haul.
The principal advantage of the big bale seems to be lower baling cost and the fact that the bales will weather reasonably well under rain if the storage ground is dry and well drained.
GRAIN HARVEST IN DRAINED VS. FLOODED FIELDS:
Comparisons of yields and drying rates in drained vs. flooded fields encourage further study. Recent developments in equipment are such that if advantages can be shown in yield and quality of rice from flooded-field harvesting, the concept should be vigorously pursued.
EVALUATION OF POTENTIAL NEW RICE DRYING METHODS
The major emphasis of six months of preliminary research was to identify specific areas needing research to improve drying of California rice varieties, including smooth- and rough-hulled lines. This goal was reached through preliminary experiments and extensive field visits to dryers. The major problem areas identified were:
þ Columnar rice dryers are currently operated at very low energy efficiencies. Depending on rice moisture content at harvest, exit air may still have enough drying potential to warrant reuse in the dryer, improving energy efficiency. Further rigorous trials are needed in both laboratory and dryers to determine the amount of air that can be efficiently used.
þ New dryer configurations now in use in the Midwest on other crops, such as the concurrent flow system, counter-current flow system, and other innovative designs need critical evaluation in terms of energy requirements and applicability to rice. This goal requires experiments with pilot-scale equipment and computer-aided simulations of rice dryers. Computer programs are currently being written for various rice dryer configurations. These simulations will help identify the needed basic data for improved dryer design and evaluations.
The moisture content at which rice should be transferred from a column dryer to a deep-bed dryer to complete drying must be determined. Computer techniques can be used for optimizing energy use and head quality during drying, both of great importance.
Energy sources other than fossil fuel need serious consideration for dryer operation. The predicted shortage of certain fossil fuels emphasizes the need for further research on methods of extracting the energy content of rice straw and hulls for on-farm energy-producing uses such as crop drying.
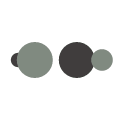